CASE STUDY
Gold Contact Slip Rings | Why Gold-Plate a ROTOCON?
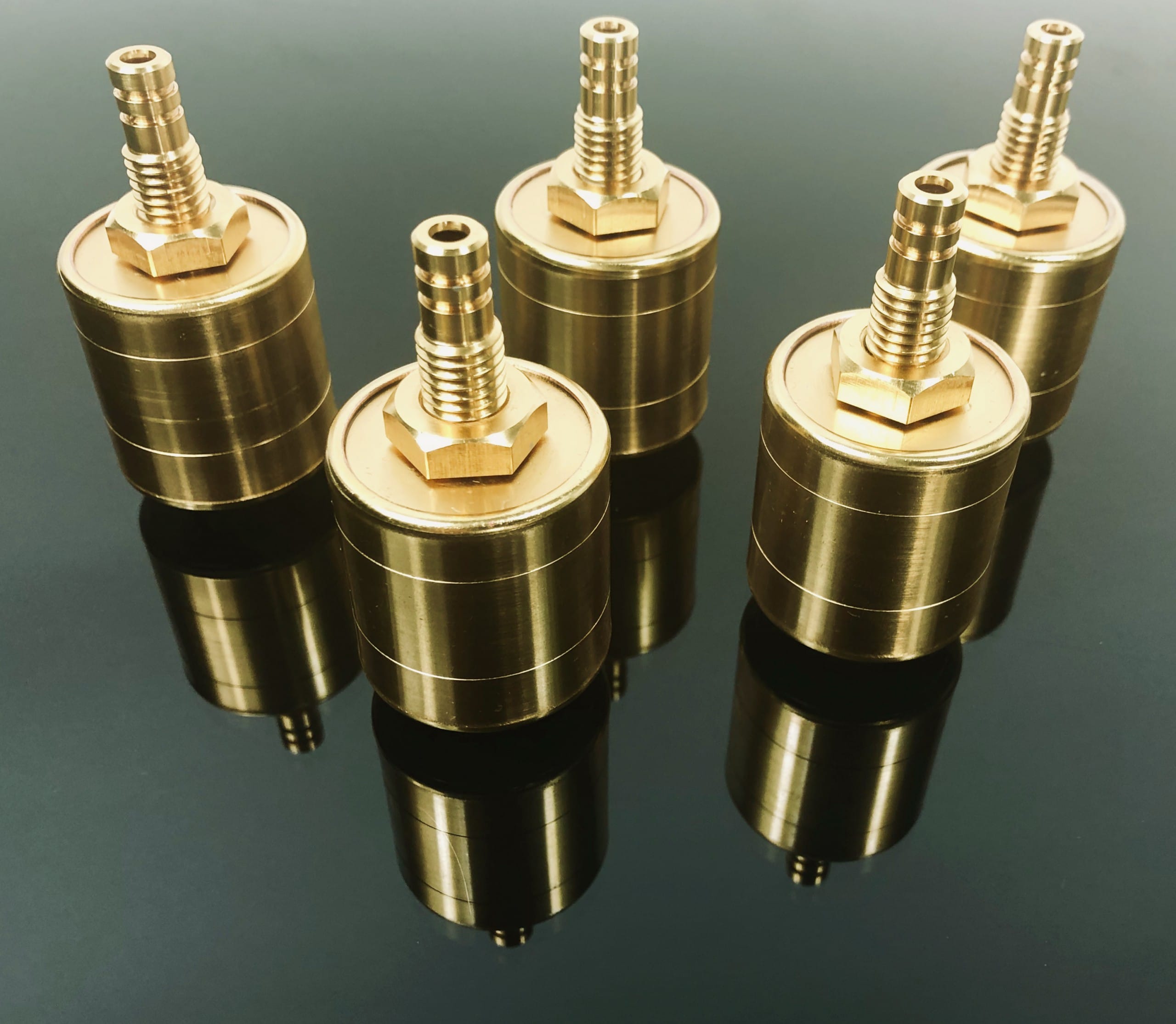
Rotocon Brushless Slip Rings vs Gold Plated Contacts
Many manufacturers of conventional brushed slip rings will advertise ‘gold plated contacts’ – but what exactly does that mean for a slip ring?
Part functional, part advertising buzzword, ‘gold plating’ a contact in a slip ring is about the best manufacturers can do to provide the highest quality connection for low noise and low contact resistance in a rotating electrical connection. Typically, standard brushed slip rings rely on a carbon (or metallic fiber) brushes to come in contact with a ring that rotates – hence the term ‘slip ring’. Carbon is a material, that while electrically conductive to a point, is electrically noisy and degrades over time producing dust and particles to a slip ring. This, in turn, will only generate more electrical resistance thus producing more heat (if higher current is being transferred) and compromising the signal integrity. A compromised signal might mean a temperature measurement is incorrect, an encoder signal is wrong, or packets/bytes of Ethernet (or any other communication protocols) are being lost along the way.
Unfortunately, gold (or silver) contacts are the crème de la crème of slip rings and they still have issues of brush wear, high & varying electrical resistance, and periodic maintenance required to sustain performance.
These issues are all forgone by using Meridian Laboratory’s unique and proprietary brushless slip ring technology which all ROTOCON rotary electrical connectors possess. By using a viscous metal mercury-wetted contact, sealed and held under oil, there is 360 degrees of electrical contact providing uninterrupted electrical continuity. Additionally, by being sealed under oil and zero metal-on-metal contact, the connection maintains a much lower and stable electrical resistance level unaffected by momentary RPM, total revolutions, vibrations, temperature variations, and many other application/environmental factors which commonly plague conventional, brushed slip rings…even ones which are gold or silver plated.
So, while conventional brushed slip rings have their place in providing a rotating electrical connection in low rotation, and non-critical applications – most industrial and production environments can be hampered by the inconsistencies these types of slip rings provide in electrical performance. Additionally, users must rely on routine slip ring maintenance which can mean cleaning out the assemblies, or replacing them periodically. This can lead to unpredictable downtime and costly losses in continuous use, production environments.
Meridian Laboratory customers who have used and trusted brushless ROTOCON rotary electrical connectors have enjoyed faster duty cycles, increased longevity, and substantially less maintenance compared to traditional, brushed slip rings.
Supreme Corrosion Protection (Gold Plated ROTOCON)
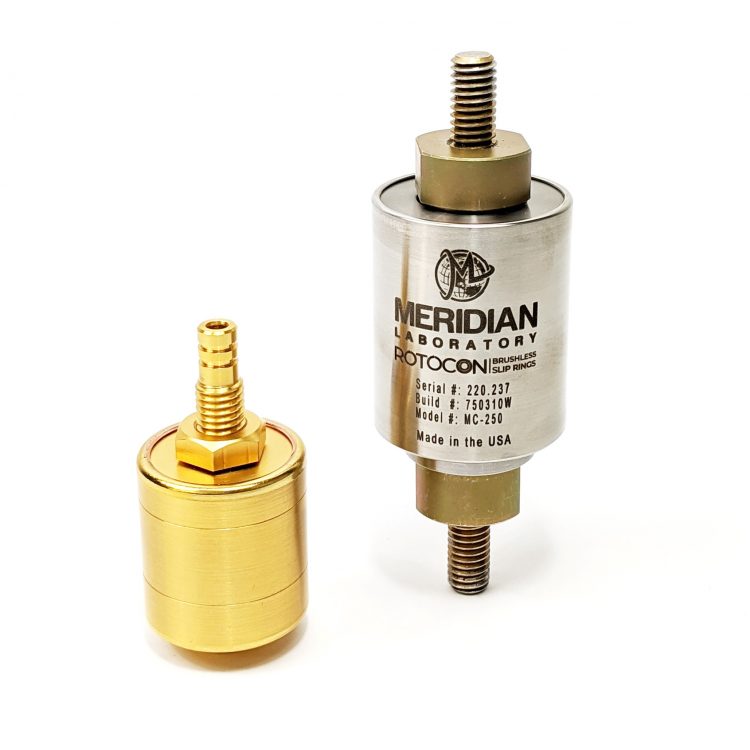
At this point you might be asking yourself, “so why gold plate a ROTOCON?”
Great point! While Meridian Laboratory doesn’t need to rely on gold plating for signal quality and low electrical resistance – gold makes for an excellent material for harsh and corrosive environments. This gold plated ROTOCON was custom designed and built for a semiconductor manufacturer, completed in under 8 weeks to serve as a high current rotating ground while allowing a vacuum to be pulled through the center of the spindle hole during rotation. Despite operating at 1500+ RPM and in an acidic, corrosive environment – Meridian Laboratory’s ROTOCON rotary electrical ground provides over 125A of current carrying capacity!
In conclusion, while aesthetically impressive, not all ROTOCON rotary electrical connectors need to be gold plated to provide an excellent electrical connection under rotation. Exceeding expectations on this challenge is another example of why Meridian Laboratory has remained an industry leader since 1963.
Innovation
We continue to reengineer, rethink, and redefine the limits of what slip rings can do, and with over 6000 standard slip ring assemblies, we’ve got the products to prove it. Whether it’s harsh environment slip ring assemblies custom engineered to your specifications, or just an expert analysis of your process to breakdown bottlenecks and make recommendations, we pride ourselves on delivering solutions our competitors simply can’t.
If our vast array of in-stock slip rings does not meet your design needs, our engineers are ready create a solution to meet any design requirements. Contact us today.