Blog / 2017.11.08
VIDEO – Contact Resistance Is Important In A Rotary Ground/Welding Clamp
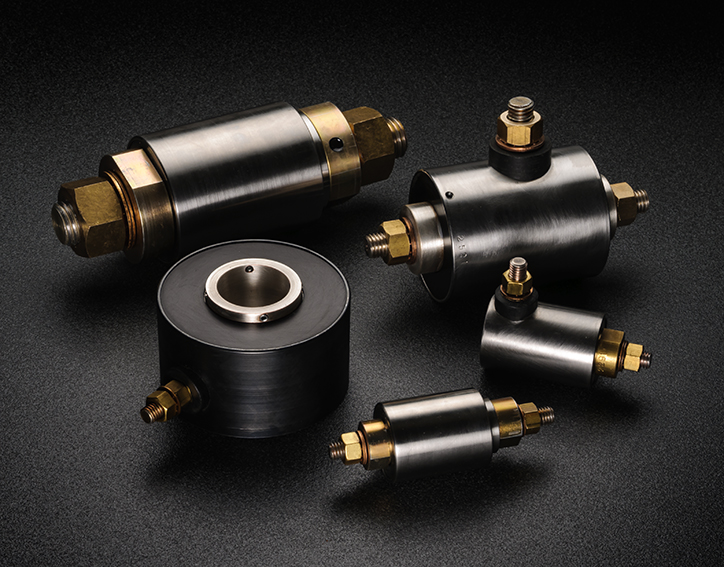
An important concept in the design and use of rotary ground clamps is contact resistance. Contact resistance is the measurement of electrical resistance between two points. Everything electrically conductive has some amount of contact resistance, typically a more conductive material will exhibit less contact resistance. ROTOCON rotary ground clamps for Meridian Laboratories exhibit properties that make them exhibit less resistance than competitors and more consistent in how that resistance is exerted. By delivering a consistent and stable current delivery, Meridian Laboratory products ensure improved results and a lower margin of error. In the video below, you will see this is the case.
After more than 55 years of success, Meridian Laboratory has developed the ability to create custom solutions that can serve any industry, project, or environment and has learned to excel at developing precisely optimized solutions for customers. Our wide range of electrical and mechanical solutions continuously helps manufacturers, engineers, and machine builders solve complex problems. If you have a need, we can build a solution.
For more information about ROTOCON you can either visit the ROTOCON product page, the ROTOCON MC-Series page, or Contact Us directly.
More Information:
ROTOCON Rotary Ground Clamp
Contrary to conventional belief, not all rotary ground clamps are the same! Conventional rotary ground clamps rely on a rudimentary principle of a ring or band of conductive material (typically copper, brass, or bronze) held around a rotating conductive stud (also usually of similar materials). To lessen the amount of friction between the two surfaces and minimize oxidation from occurring, some manufacturers will supply conductive grease which is gravity fed into the gap between the rotating and stationary parts of a rotating ground clamp. This makes conventional rotary ground clamps both maintenance intensive and typically messy in appearance and operation.
This type of solution may work in applications which are not often or continuously rotating, however come with a major drawback for applications which rely on continuous rotation or do rotate frequently. Aside from constantly having to refill the grease container and adjusting the pressure which the stationary band has around the rotating stud – this style of rotary ground clamp has a fluctuating range of electrical contact resistance, dependent on the number of total revolutions, rotational speed, user adjustment, and maintenance. So why is contact resistance so important?
Contact resistance is the measurement of electrical resistance between two points of a wire or a system, typically measured in Ohms or milli-Ohm for very small amounts of resistance. Everything electrically conductive has an amount of contact resistance within it, dependent on the material and the temperature at which it is being measured at. Typically the more conductive a material is, the lesser amount of contact resistance it will have. Contact resistance oftentimes becomes a significant factor in high current applications because of the loss of power dissipated (measured in watts) rules associated with electrical systems.
The technical equation for calculating the power dissipated in a system is: WattsLoss = Current 2 x Resistance. As the current draw of a system increases, it exponentially increases the amount of power or watts being dissipated in the system, even if the resistance stays the same. It’s for this reason that finding methods to lower or lessen the amount of contact resistance within a system is of utmost importance.
In this video we have set up a demonstration of two conventional rotating ground clamps operating in series (to allow for the rotation and measurement of them) against two ROTOCON MC-500 rotary ground clamps, also operating in series. A current draw of 500 amps is being transferred across the system, with both of them set at 500A while stationary.
As the conventional rotary ground clamps rotate you will see fluctuations in the current draw, dropping below and then greatly exceeding the initially set 500 amp level. With the conventional rotating ground clamps the current varies as much as over 100 amps; in a welding application this amount is the difference between poor penetration and holes being burnt into your work piece. This fluctuation in amperage draw is due to the varying amount of contact resistance which the rotary ground clamps experience while under rotation.
In the same test fixture are two ROTOCON MC-500 rotary ground clamps with a 500A draw being transferred across them, in the same method as before. From its unique design, all ROTOCON rotary ground clamps exhibit low and consistently stable electrical contact resistance – regardless of RPM, total revolutions, or temperature. Even after hours of rotation, the amperage stays consistently at approximately 500A with very little fluctuation.
At this point, you might be asking yourself why is this so important? While the exact reason is oftentimes application dependent, it is universally understood that the lower and more stable the contact resistance of a system is – the more consistent and stable current delivery you will see and better results you will have from it. Regardless if the end goal of an application is a weld between two metals, an even film of material deposition in an electroplating application, or simply getting the most efficient delivery of current between a rotating and stationary portion of a machine. This consistent and stable current delivery provides a more consistent process, improved results, and a lower margin of error. Occasionally, depending on the current draw and amount of usage, a MC-Series rotary ground clamp can oftentimes be paid for simply by the energy savings alone which it provides for an application.