Blog / 2017.09.27
ROTOCON Thriving Through the Decades…from Cheese Slices to the Titanic
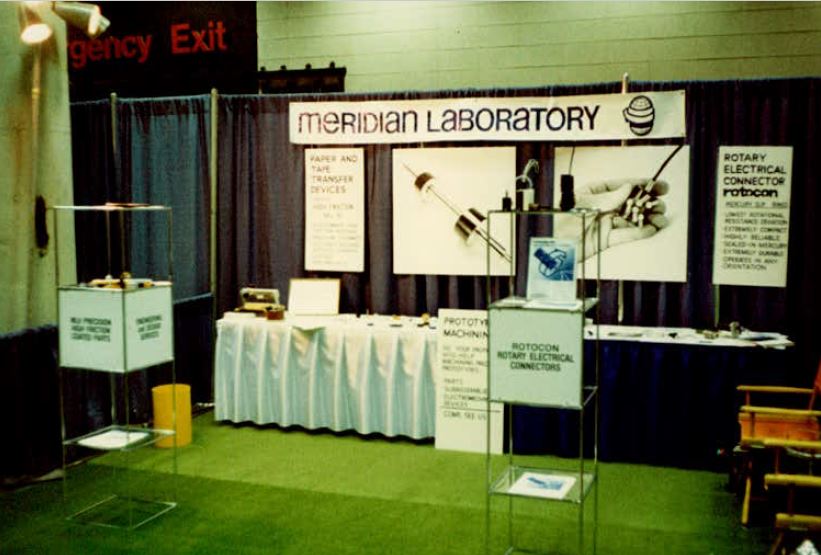
Here at Meridian Laboratory, we often boast of our company’s proud 55-year history. This however, is not the real boast; plenty of companies have been around a long time, but simply surviving is no guarantee of success. To illustrate the experience we have gained through our 55 years of delivering quality products, we have prepared a brief history of the company’s ROTOCON line, its successes, product evolution, and most importantly, a proven record of innovation to show that Meridian Laboratory has not just been surviving for more than 50 years, but thriving.
German Engineering in the 1960’s
In the early 1960’s, the founders of Meridian Laboratory realized that there was a need for slip rings in the USA, but there were not many domestic suppliers able to meet the quality of product demanded.
The founders started sourcing and selling slip rings from Germany, often tweaking and modifying designs for customers, and Meridian engineers quickly became experts at developing solutions to meet customers’ exact needs.
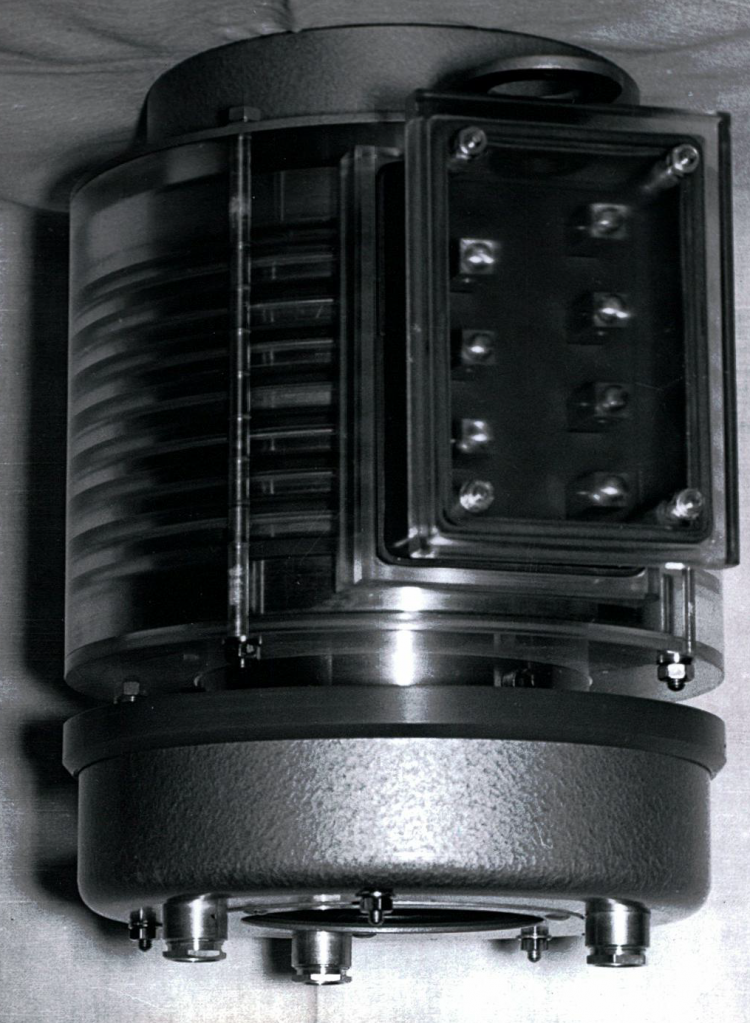
Crafting Quality Solutions in the 1970’s
A milestone occurred for Meridian Laboratory when they were approached by Kraft Foods and asked for a custom-built slip ring, which had to be designed and built from scratch. This slip ring was one of the last pieces of the puzzle Kraft needed to improve their manufacturing process enough to allow them to economically manufacture and package single-serve processed cheese, now a staple in U.S. households. The rotational speed and reliability of Meridian Laboratory slip rings allowed Kraft to make Kraft Slices at the rate of hundreds per minute. This was the beginning of the niche Meridian Laboratory would carve out in providing inventive solutions for innovative companies looking to improve their machines and processes.
As Meridian Laboratory shifted to take advantage of the growing needs of innovative companies, another milestone customer, General Electric, approached them. GE commissioned Meridian Laboratory to design and build a custom, maintenance-free, low-noise slip ring with over 100 contact points, far larger and more complex than any on the market. Meridian already had a reputation for being innovative designers, adapting common slip ring designs to create customized solutions, but this was more than that. This was designing a whole new product, and paving a whole new legacy of industry firsts and market solutions. It tested the team’s abilities, but with the successful delivery of this slip ring for General Electric, Meridian Laboratory saw the need to create their own line of slip rings and design them to be more reliable, better performing, and customizable than alternatives on the market.
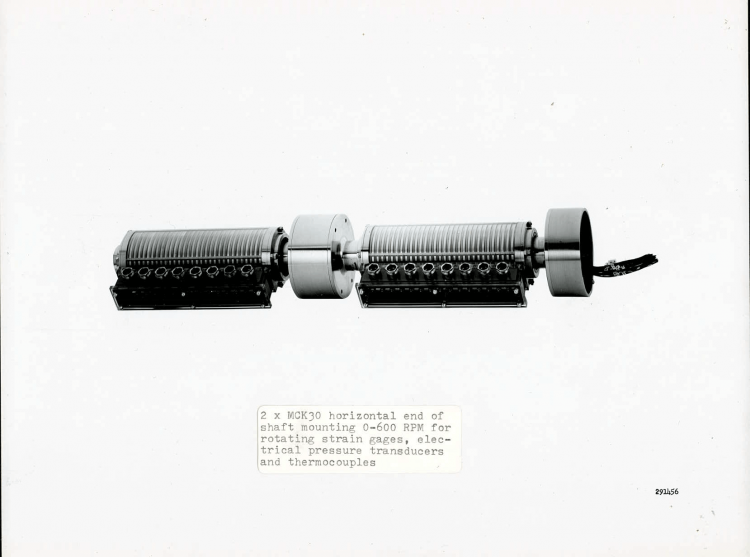
Titanic Changes in the 1980’s
The early 1980’s were greatly productive as Meridian Laboratory saw the opportunity for standard product lines (rather than custom building nearly every slip ring). The MX, MC and other standard product lines came into development fairly quickly as the need for mass standardization exploded during the 80’s manufacturing boom. Another product line, the harsh industrial and environmentally-sealed MXO series, came about a little later and had immediate success extending the capabilities and industries served by Meridian Laboratory. The signal quality of the MXO line even helped to create worldwide headlines when it was used on an oceanographic research mission, run by the Woods Hole Oceanographic Institute in 1985. The expedition was led by Bob Ballard and resulted in the discovery of the wreck of the R.M.S Titanic.
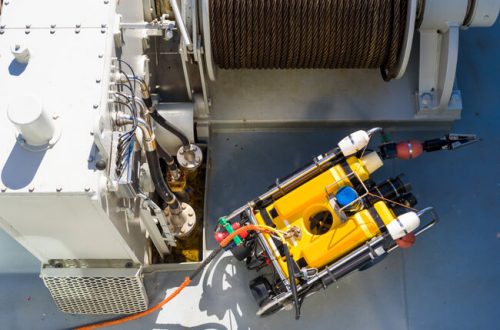
The 80’s were kind to Meridian Labs. As the spread of communications and technology drove manufacturing growth around the world, international expansion for Meridian was not far behind. Order quantities grew and product lines expanded. As Southeast Asia – Japan in particular – grew into a manufacturing powerhouse, Meridian Laboratory sold ROTOCON slip rings to drive their factories and helped power the explosion of modernization through automotive and computer manufacturing.

Slip Rings for Silicon Production in the 1990’s
As the ROTOCON product line expanded, it opened more markets for Meridian to serve. The takeoff of the personal electronics age in the 1990’s meant a huge need for microprocessors. Becoming heavily involved in serving the semiconductor industry, Meridian focused on building one-off custom units and production quantities alike, tailored for the precise needs of microprocessor manufacturing. At their height, factories powering the electronics boom ran almost non-stop, and workers were constantly checking equipment for problems that could create impurities or defects in the delicate silicon wafers. Under these conditions, the quality and reliability of ROTOCON increased in value drastically, as a defective production run could easily cost a factory $1 million in a single day.
Going Digital For The 2000s
The 2000’s marked the advent of the digital age, and machines were made to run faster, more efficiently, and with fewer maintenance intervals. The transition to high-speed internet connectivity in manufacturing created a need to adapt the ROTOCON product line to meet the needs of new communication protocols. To improve efficiency and output, companies integrated programmable logic controllers (PLC) and high-speed data into their production machinery. Again, Meridian Laboratory’s ability to anticipate and adapt to market changes and technological advancement opened doors for the ROTOCON product. Meridian Laboratory engineers developed one of the first Ethernet compatible slip rings in the world, a jump from analog to digital signals akin to the jump between telegraph communication and the telephone. From there, Meridian developed product lines that meet and exceed the needs of digital communication and integrated manufacturing tools, supporting communication protocols such as Ethernet (10/100/1Gbps), Etherlink, LAPPNET, ProfiNet, Profibus, ControlNet, DeviceNet, CAN-Bus, RS485, RS422, USB (1.0/2.0), Modbus, EtherCAT, CC-Link, and many others.
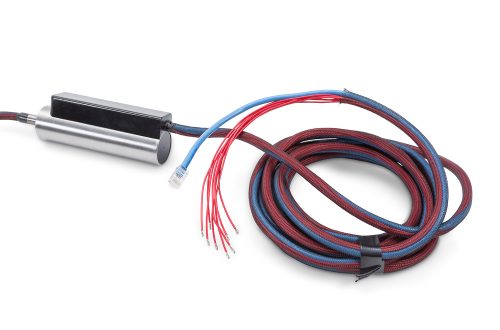
The Future of ROTOCON
Up until 2012, Meridian relied on subtle changes in market demands to determine where product development was going. Since then they have returned to their roots by designing and building customized slip rings with distinct applications for unique purposes and environments. Meridian aims to be the go-to solution for special situations under which conventional brushed slip rings simply cannot perform. Current innovations include high speed, high voltage, high current, high frequency slip rings and the ability to integrate with other rotary solutions, FORJ’s (Fiber optic rotary joints), encoders, and rotary unions. After more than 55 years, Meridian can create custom solutions to serve any industry, project, or environment and excels at developing precisely optimized solutions for its customers.
Our wide range of electrical and mechanical solutions continuously helps manufacturers, engineers, and machine builders solve complex problems. If you have a need, we can build a solution. Contact us!